The Following was taken from a copy of the “Lighting Bolt” from April 1986. Retrieved and transcribed by Dana Fellows ~ 2011
Northwestern Takes Bold Step Into Future
The year 1879 was the year in which the curious minds and restless hands that would lead America into its age of greatest progress were beginning to make their presence felt.
This was the year in which Thomas Alva Edison would perfect his electric light in Menlo Park, New Jersey and when inter-city telephone communication would be demonstrated for the first time. In that year Northwestern Barb Wire Company made its quiet entrance on the local scene.
Four young and industrious hardware merchants, headed by Washington M. Dillon and his stepbrother, William C. Robinson, signed papers of incorporation of Northwestern Barb Wire Company – thus beginning the history of Northwestern Steel and Wire Company on that cold day on February 28, 1879.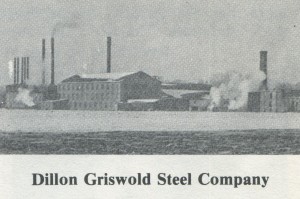
Ironically also in that same year, an Englishman named Dugald Clark would, for the first time, melt steel in a furnace that utilized an electric arc .. a process that would be perfected to a high-degree of efficiency at Northwestern Steel and Wire Company 57 years later.
At the outset, 10 employees turned out spools of barb wire in a single three-story building built from stone quarried from the Rock River and positioned along the river banks on the Rock Falls side.
The Company purchased the smooth wire it needed from the American Steel and Wire Company in DeKalb. About 600 spools of barb wire a day were being turned out at the Company’s modest facility. Power to run the barb wire machines came from a long-line shaft driven by water wheels installed on the river side of the mill race.
Into The 20th Century
Washington M. Dillon was forced to continue the operation of the plant on his own following the sudden death of William Robinson in 1883. In 1892, Washington Dillon entered into a new partnership with J W Griswold and started the Dillon-Griswold Wire Company in Sterling. Dillon kept his original plant across the river in Rock Falls, but devoted much of his time and energy to the new organization, which manufactured Dillon’s barb wire and Griswold’s bale ties, and later added field fence and nails to the product line.
The new firm grew and prospered until Griswold’s death in 1902. When Griswold’s heirs expressed little interest in managing the factory, Dillon … dissolved the partnership and returned to the operation of Northwestern Barb Wire Company in Rock Falls.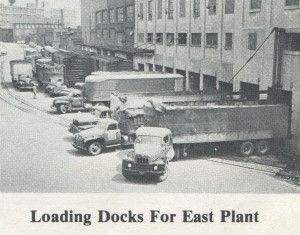
When the Dillon-Griswold Company went into receivership in 1912, Northwestern purchased the remaining assets of the firm and the barb wire factory moved from Rock Falls into the Sterling plant’s newer and larger facilities.
The elder Dillon was assisted in the move by his son, Paul W., who had, at that time, been assuming additional responsibilities in the firm for the past few years. Following Washington’s death in 1920, Paul – P W. to his friends and associates – was elected president by the board of directors. He was an intense, capable young man whose leadership and enterprise quickly became apparent to those around him in the Company and in the community.
In 1930, the third generation of the Dillon family in Northwestern management, W.M. (Martin) Dillon, was named general manager of a newly acquired subsidiary firm: Parrish-Alford Fence and Machine Company of Knightstown, Indiana. Martin ran the firm for five years at its Indiana location, then supervised the moving of the facility back to Northwestern’s original home in Rock Falls.
Northwestern faced some difficult times in the decade of the 1920’s and 1930’s. A major fire swept through the wire mill, causing three fatalities and doing an estimated quarter-million dollars in damage during the 1920’s. But at this time in Northwestern’s history, the greatest threat to its future was not represented by natural causes, but by man-made ones.
During the hard times that followed the stock market crash of 1929, the Company felt the economic pinch even more than the majority of the other he country, NSW was operating at full capacity to assist the war effort.
When Leonard Shannahan (who later went on to become Superintendent of the IO-Inch Mill) first came to Northwestern in 1946, the Company was pouring steel into I-ton ingots. “In 1947 we averaged 500 tons a day on that mill,” Leonard recently reflected. “That eventually went up to 1100 ton a day.”
Leonard said he misses those days when spirit among workers was high and there weren’t so many restrictions on job descriptions. “You knew· everyone – their wife’s name and kids names. We were close. When you walked into the IO-Inch Mill on a given day, you didn’t know what job you would eventually be doing. If we had a breakdown everybody worked on it. It didn’t matter who you were.”
In the early 1950’s the Company embarked on yet another major expansion in the building of a complete new plant just west of Avenue G to house two new 150-ton electric furnaces, a new 46-inch blooming mill and a 12-inch merchant bar mill.
By 1968 technology was starting to work in Northwestern’s favor A new concept developed by the Company, called ultra-high power, allowed NSW to achieve substantial increases in productivity This year saw the installation of a 250-ton furnace.
In just three years, Northwestern’s insatiable appetite for steel melting power increased to the point that in 1971, the first heat of steel was tapped from furnace No.7, – a 400-ton unit that remains the largest of its type in the world. By the end of the decade, a second 400-ton furnace was installed and the 250-ton furnace also was converted to 400-tons.
How It’s Done Today
When it comes to steel production through the use of electric furnaces, no one “does it better” than Northwestern Steel and Wire.
A pioneer in electric steel-making, Northwestern has continually stepped up its production capacity to include three 400-ton electric furnaces .. the largest of their kind in the world.
Why does Northwestern use electric furnaces to melt scrap steel instead of producing steel from scratch? There are a number of reasons:
(1) Northwestern is located in a good scrap area and selected steel scrap is the principal ingredient for the production of electric steel.
(2) Northwestern is located in an area where there is more than adequate electrical supply This is vitally important to the mill, as its daily usage of electricity is comparable to the electrical needs of a city of 300,000 population.
(3) Electricity is considered a “pure” source of heat, and does not in itself impart any mysterious properties to the steel. Heat comes from both the proximity of the electric arc and the electrical resistance of the steel bath itself The production of heat by electricity is unique in that oxygen is not necessary to support combustion. Thus, the quantity of oxygen can be controlled, and the presence of oxygen compounds and other impurities undesirable in good steel can be materially reduced. In addition, the electric furnace process permits the addition of alloying agents to molten steel without appreciable loss by oxidation.
(4) Northwestern has 50 years of experience in the electric steel-making process.
The operation begins with steel scrap, sorted by grade and loaded into huge charging buckets which are used to transfer the scrap to the furnace. The furnaces themselves resemble giant tea kettles on rockers; their steel shells are lined with refractory or water cooled panels to hold steel reaching temperatures of 3000-degrees. The dome-shaped, water cooled roof of the furnace is removable in that it swings aside when the furnace is to be charged with scrap. Once the furnace has been charged, the roof is swung back into place and three carbon electrodes are lowered into the furnace.
In the case of the 400-ton furnaces, these three electrodes are 28-inches in diameter It is at this point that ultrahigh power is supplied to the electrodes through automatic control devices connected directly to Northwestern Steel and Wire Company’s computer.
Current within the furnace arcs from one electrode to the metallic charge of scrap and from the charge to the next electrode. This process continues until the steel is a molten mass. Periodically during the heat, limestone and flux are added to the molten steel causing impurities to rise to the surface and form the slag which floats on top of the metal. At intervals during the heat, the furnace is tilted slightly so that this slag can be removed.
When the temperature of the bath reaches a specific point, alloying elements are added to the heat to determine the grade of steel as called for in the specifications given to the chief melter.
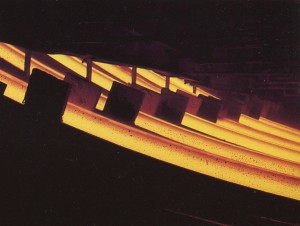
Bloom Caster
When the steel is ready for tapping, the electrodes are raised above the dome and the tap hole is opened. Awaiting the molten metal is a ladle into which the steel is to be poured. The ladle is pre-heated at a pre-heat station so that the molten steel will retain its high temperatures throughout the casting process. Since the electric furnace is on rockers, it can be gradually tilted so that the steel is drained from under the remaining slag.
Most of the steel that Northwestern produces is processed either into a bloom or billet continuous caster a relatively new process that takes the place of the old billet mill. Northwestern utilizes an 8-strand billet and 6-strand bloom caster, which means that either eight billets or six strands are produced simultaneously as the steel is poured through the caster. The billets and blooms are then taken to one of Northwestern’s rolling mills where they are reheated in a reheat furnace and then, while hot and pliable, rolled into finished products, such as angles, flats, channel, beams and rods.
Making Steel – The Electric Way
By the time the German Army invaded Poland in 1939, Northwestern had nearly recovered from the financial struggles involved in the start-up of the new steel plant and was well into a tone of continuing expansion, improved product quality and increasing profits.
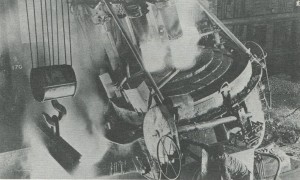
Northwestern's 10 Ton Furnace, about 1936
The two original 10-ton electric furnaces at Northwestern allowed the Company to produce its own steel and wire rod and thus become self-sufficient for the first time.
Ingots poured from these first furnaces were about 6×6 inches and weighed about 800 pounds. They were poured into gang molds, each holding four ingots. The ingots later were increased to 12×12 and weighed about 1,400 pounds.
Fryn Engineering designed a small re-heat furnace for the ingots and the blooming mill reduced them to 2×2 inch billets.
Next step in the process was a rod mill to produce the No.5 rods from the billets. This was a new mill designed by Fred Gildon, Superintendent of the Rod Mill, and the manufacturer, Birdsboro Corporation. Gildon is credited with being a genius in this area.
An innovative feature of the mill was the continuous production of a round with a minimum of handling, thus requiring a very small labor force of 8 to 10 men. It also produced rods at speeds almost unheard of at that time – 3,700 feet / minute (by contrast, Northwestern’s existing Morgan Rod Train is listed at 20,000 feet/minute). At full capacity, it would produce about 30 tons an hour.
As a pioneer in the electric steel making process, Northwestern’s melt shop had to proceed by trial and error. One of Northwestern’s early successes, though, was called top-charging. The idea of top-charging an electric furnace is believed to have originated in the development of these first furnaces for Northwestern. The earlier furnaces used elsewhere, were side-charged units, which were alright for making alloys and special steels.
But in order to get any tonnage volume out of the furnace, it was necessary to get a lot of scrap into it in a short period of time, so the top charge arrangement was perfected.
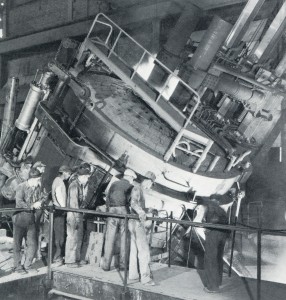
Northwestern's 50 Ton Furnace, about 1940
Northwestern continually upgraded its steelmaking capacity. By the early 1940’s Northwestern installed two 50-ton furnaces, and, like the rest of plied rod to Northwestern were also competitors in the wire business. To get away from this potentially disastrous situation, Paul Dillon knew he had to begin melting steel and making his own rods; but he was apparently blocked by a new piece of legislation called the National Recovery Act.
In the midst of the Depression, Congress had decided that there was an over-abundance of steel production in the country and banned the installation of any additional facilities. The Act was later found unconstitutional, but at the time, it presented the greatest challenge ever to the survival of Northwestern Barb Wire Company.
Paul Dillon’s solution to the problem posed by the National Recovery Act was to use the wording of the NRA’s section on steel to his advantage. The Act prohibited “the construction of blast furnace, open hearth or Bessemer steel capacity,” but neglected to mention electric furnace steelmaking.
Although it had been used only for small quantities of specialty steels, the electric furnace offered Northwestern the chance to get into steelmaking.
Working closely with William Moore of Lectromelt Corporation, a pioneer in electric furnace steelmaking, and with engineers from Westinghouse Corporation, who built the necessary electrical equipment, Paul Dillon drove Northwestern through the legal loophole in the NRA and installed two small 10-ton electric furnaces at the Sterling plant, along with a billet mill and a rod mill after a horribly cold winter.
Ignoring the experts who said carbon steel could not be made profitably in electric furnaces, Northwestern, on Easter Sunday, April 12, 1936 became a steel producer as well as a wire mill … and continues to this day to be at the forefront of electric furnace technology.